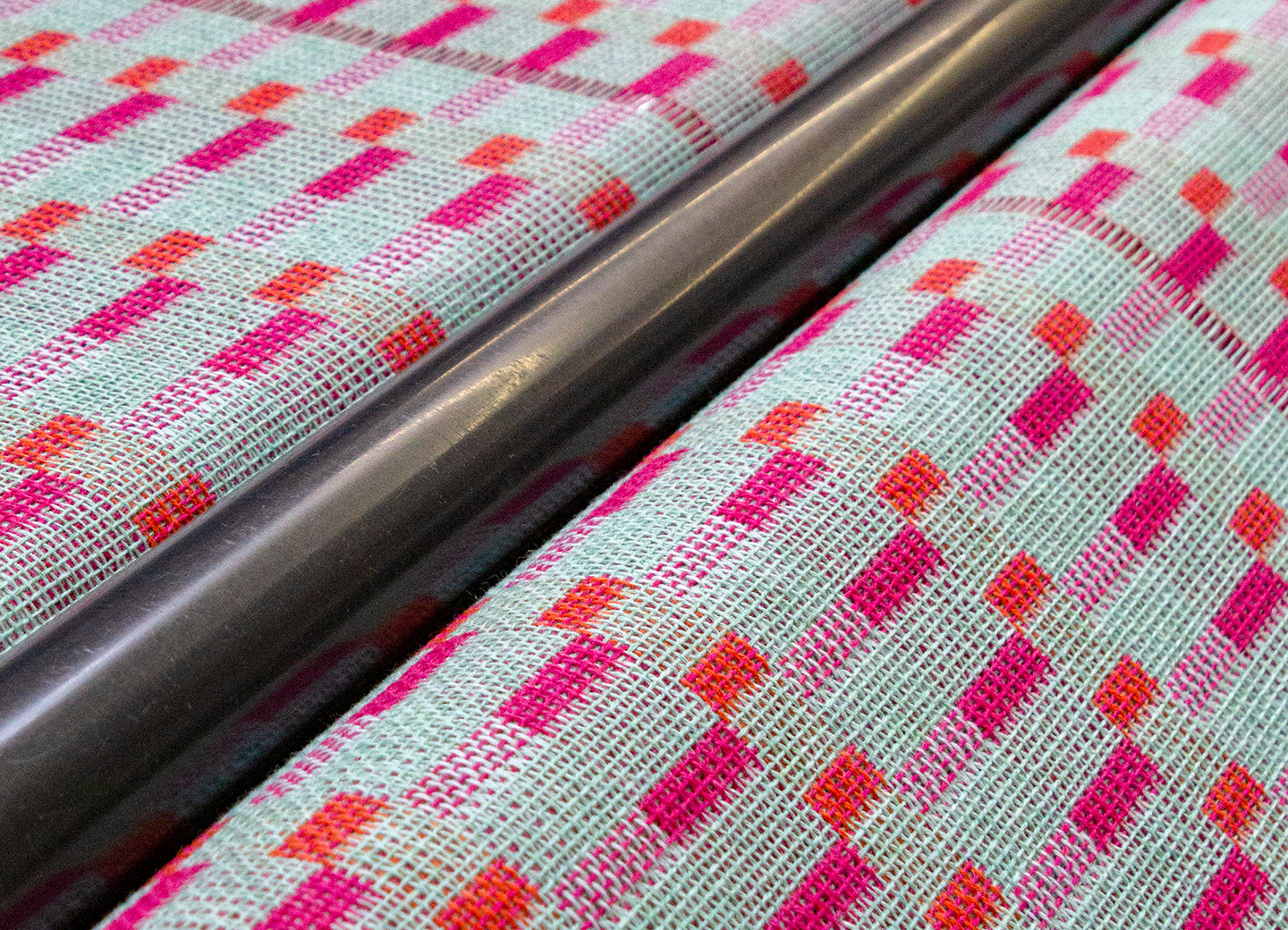
Woven Textile Designer Award - Winning Design in Production!
Launched in 2017, our Woven Textile Designer Award sought to uncover the best of new textile design talent by inviting current students and recent graduates to submit innovative and contemporary designs that pushed boundaries.
From a shortlist of six designs, the winning design was chosen by a top judging panel as part of Edinburgh International Fashion Festival - Fleet Bigwood, Alistair O’Neill, Fabio Piras, Clements Ribeiro, and Rachel Meddowes.
The winner, Jessica Cutler, was announced at Scotland Re:Designed annual awards and runway showcase in Glasgow on November 9th, 2017.
Recent graduate Jessica Cutler, who studied Textiles in Practice at Manchester School of Art and graduated in July 2017, was presented the award for her design ‘Devon Seasons’.
Jessica said: “I’m delighted to have won this award. It was a great evening at such a great venue. Glasgow’s an amazing city – it’s got such a vibrant creative scene which seems to be really well supported. Thanks again to everyone involved for this opportunity. I’m looking forward to working with Knockando Woolmill and can’t wait to see the finished product!”
As well as receiving £500, the winning design is currently being woven by the Woomill (scarves and blankets) and will be sold with a custom label featuring the designer’s name.
We are looking forward to welcoming Jessica down to the Woolmill tomorrow (19th July) to see her winning design in production.
Pre order the limited edition scarves and blankets now.
Here's a look at the scarves in production...
1. Winding
Yarn cones are prepared for the warp (vertical threads) in a cylindrical form - a process that involves transferring yarn from one type of package to another. Further functions of winding are to inspect the yarn quality and to clear any defects.
2. Warping
Warping is the preparation of the warp threads (known as ends) which run vertically from the top to bottom of a piece of fabric.
The warp cones are placed onto a frame called the creel in a pre-determined colour pattern - the number of threads in the warp varies according to the fineness of the yarn and the density and width of the fabric required. The yarn from the creel then passes through a leasing reed which separates the yarn threads and keeps them in the correct order. The warp threads are then wound onto a warping drum (a large steel cylinder) - at the Woolmill warping is carried out on a sectional machine where each section of warp threads are wound onto the warping drum alongside previous sections. When the desired amount of yarn has been added, the warp is removed from the drum and is transferred onto a warping beam. The weaving process is then ready to begin.
4. Beaming and Drawing in
In order to create woven textiles with different structures, each thread has to move in a specific order. In order achieve this, the warp is drawn in thread by thread through the eyes of the heddle on the shafts. These shafts are raised and lowered in the loom to determine the warp and weft interlacing. Warp threads are then pulled through the teeth of the reed (a reed secures the weft in place as it is woven in)
When we weave scarves, throws, or fabric with the same structure, the drawing in stage can be skipped. Each thread is tied to the corresponding warp thread that is ending in the loom.
4. Weaving
Weaving is the introduction of the weft yarn, known as picks which run horizontally across the fabric.
Here at the Woolmill, a power loom is used - a mechanised loom powered by a line shaft. Within the Power Loom category, there are many productions, usually named after the designer - the Woolmill owns two Rapiers. This type of weaving is very versatile because a rapier loom can weave using a large variety of threads. There are several types of rapiers, however they all use a hook system attached to a rod that passes the pick across the shed. A Rapier loom can reach up to 700 picks per minute depending on the type yarn!
Pre order the limited edition products now.